Stepper motors consists of two varieties; unipolar or bipolar. Bipolar motors are the strongest type of stepper motor and usually have four or eight leads. They have two sets of electromagnetic coils internally, and stepping is achieved by changing the direction of current within those coils. Unipolar motors, identifiable by having 5,6 or even 8 wires, also have two coils, but every one has a centre tap. Unipolar motors can step without having to reverse the direction of current in the coils, making the electronics simpler. However, because the centre tap is used to energise only half of each coil at a time they typically have less torque than bipolar.
Stepper Motors Design
Step motors are called “digital motors” because they move in steps, like the hands on a clock. When the first coil is energized, the rotor teeth align with the teeth in the first stator winding and hold position. When the second winding is energized, the teeth in the rotor move slightly and align with the second stator winding and hold position. The total movement in this example is one full step.
There are usually 200 steps per revolution, each step being 1.8°.The step motor was made possible by the development of electronic step motor controllers. Electronics are required to energize the windings with proper voltage and current, with the proper phase, in the right sequence, at the right time. Controllers have evolved to be able to move step motors in as many as 20,000 steps per revolution, providing 100 times finer movement (0.018° per step).
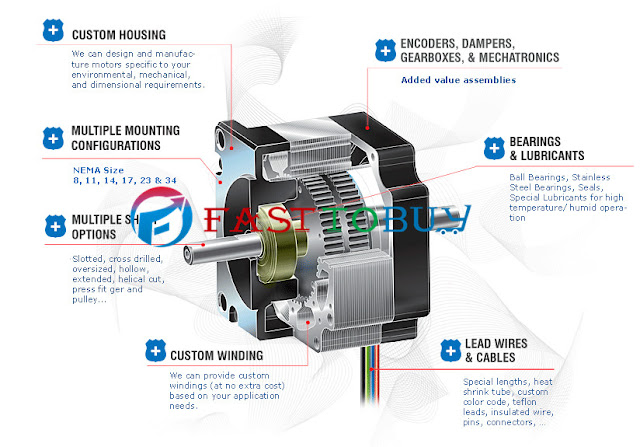
Stepper Advantages:
Stepper motors offer several advantages over servo motors beyond the larger number of poles and easier drive control. The design of the Stepper motor drive offers a constant holding torque without the need for the motor to be powered.
The torque of a stepper motor at low speeds is greater than a servo motor of the same size. One of the biggest advantages of stepper motors is their relatively inexpensive and availability.
Stepper Limitations:
- Low Efficiency – Unlike DC motors, stepper motor current consumption is independent of load. They draw the most current when they are doing no work at all. Because of this, they tend to run hot.
- Limited High Speed Torque - In general, stepper motors have less torque at high speeds than at low speeds. Some steppers are optimized for better high-speed performance, but they need to be paired with an appropriate driver to achieve that performance.
- No Feedback – Unlike servo motors, most steppers do not have integral feedback for position. Although great precision can be achieved running ‘open loop’. Limit switches or ‘home’ detectors are typically required for safety and/or to establish a reference position.
Snowitmotor supply both hybrid stepper motor and brushless AC servo motors and drives for machine automation. We do not supply DC brushed servomotors and drives which are older technology. Both steppers and brushless servomotors are similar in construction but the servomotors have feedback devices which enable closed loop operation. There are a lot of varying opinions about the pros and cons of either style of motor, so this can help you decide which to use. It isn't as easy as one being much better than the other. Overall machine functionality is highly determined by the controller and software and is more important than just comparing one style of motor with the other.